How EDI can automate your procure-to-pay cycle
The procure-to-pay (P2P) cycle allows businesses to inquire about, request, receive, and pay for goods and services. Most P2P cycles involve several stages:
- Request for price/request for quotation (RFP/RFQ): A business requests suppliers to provide pricing, product specifications, payment terms, and other information on goods and services they wish to purchase.
- Supply management and vendor selection: The business researches potential suppliers to ensure that the best available vendor is selected.
- Requisition and purchase order (PO): The business internally approves a “request to buy” and produces an “authorization to buy” by way of a PO document that includes details like items, prices, quantities, destinations, and other requirements.
- Receiving and invoice reconciliation: The business accepts the physical shipment and updates inventory, tracking, and accounting records. The invoice is compared with the authorization to buy (PO) and the receipt of the goods (ASN) in order to ensure accuracy and agreement across the three parts. This is also known as a “3-way match”.
- Accounts payable: Having reconciled the purchase order and the goods receipt, the business authorizes payment. Any discrepancies between the goods ordered and the goods received is noted and decremented from the payment along with any other promotional marketing dollars attributed to the exchange of goods.
EDI and procure-to-pay automation
A paper-based P2P cycle involves a lot of manual steps, including the review of PO, receipt, and invoice documents:
- The buyer queries its inventory system to identify orders that need to be placed.
- The buyer creates and submits an RFP/RFQ to listing websites or specific suppliers via email or conventional mail.
- After receiving and evaluating responses to its RFP/RFQ, the buyer enters relevant data into its purchasing system, creates and prints a PO, and mails it to its preferred vendor.
- A few days later, the vendor receives the PO, creates an order in its order management system, and mails an order acknowledgement back to the buyer.
- The supplier picks the order, creates shipping documents, calls the carrier, prints an invoice, and encloses the invoice with the shipment to the buyer. The buyer manually receives the goods against the PO using the shipment documents, and then manually enters the invoice into its accounting system.
The manual process can take anywhere from 7 to 10 days, including the time it takes to send and receive documents, validate them, and enter them into the appropriate systems.
An EDI can automate these processes and largely eliminate the need to communicate by phone, fax, or email:
- The EDI solution queries the ERP system automatically to identify stock in need of replenishment or purchases that need to be made.
- It creates a “Request for Quotation (840)” and submits an RFP/RFQ to known suppliers and third-party listing organizations.
- The buyer receives a notification from its EDI solution that relevant quotes from potential suppliers are available in its purchasing system. The buyer approves a PO for the preferred vendor, which is then sent to the vendor automatically.
- The supplier receives the EDI message, sends back a “Functional Acknowledgement (997)”, and parses the PO data into its order management system. An EDI “Purchase Order Acknowledgement (855)” is automatically generated, which is sent back to the buyer to confirm the order, products, quantities, pricing, and expected delivery.
- The supplier’s ERP system is updated with the customer’s order. The ERP system validates product availability, pricing, and requested shipping dates, and then automatically creates pick and pack sheets for the warehouse. When the shipment is made, it automatically generates a “Motor Carrier Shipment Pickup Notification (216)”, an “Advance Ship Notice (856)”, and an “Invoice (810)”, and sends them via EDI to the appropriate parties.
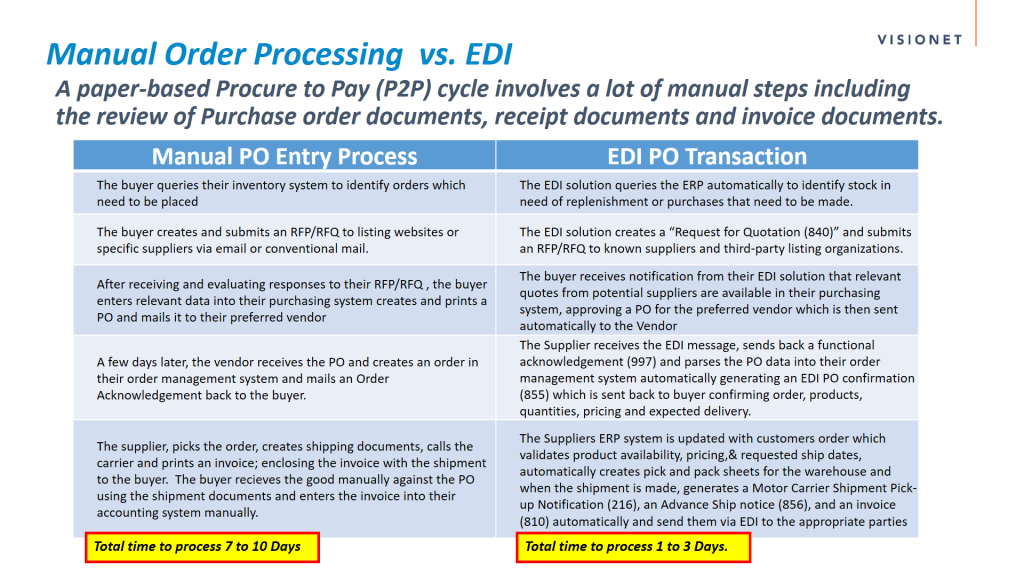
An EDI-automated procure-to-pay cycle requires much less human intervention, works extremely efficiently, and is much less susceptible to human error. The total processing time is 1-3 days compared to 7-10 days for the manual P2P cycle.
Some of the specific advantages of EDI automation in the P2P cycle include:
- PO Processing: Sending and receiving POs through EDI improves speed and accuracy of the transaction by eliminating keystroke errors and reprocessing costs associated with data rekeying. EDI ensures that your trading partners receive your error-free POs directly. You no longer need to allocate staff and other resources for order processing, freeing them up to focus on customer service instead of manual data entry.
- Replenishment: A well-designed, well-implemented EDI solution can automatically generate and send POs using features that already exist within many ERP systems like reorder points (ROPs), i.e. when available-to-sell (ATS) quantities dip below a predefined threshold.
- Audit and Compliance: When all your orders and invoices are electronic, the transactions automatically create an audit trail. This helps compliance by ensuring that payment verification can take place accurately and completely. The 3-way match between PO, ASN, and invoice helps make vendor payments in a timely and efficient manner.
Conclusion
Using EDI to automate your P2P cycle will help your organization boost operational efficiency, shorten time to market, and eliminate costly errors and rework. EDI solutions like PartnerLinQ can automate paper-based, flat-file, and API processes and bridge the gap between traditional and non-traditional EDI transaction structures by integrating data from trading partners into your company’s enterprise system and business processes.
If you’re interested in taking advantage of these benefits by adding EDI to your P2P cycle, get in touch with a PartnerLinQ expert today.